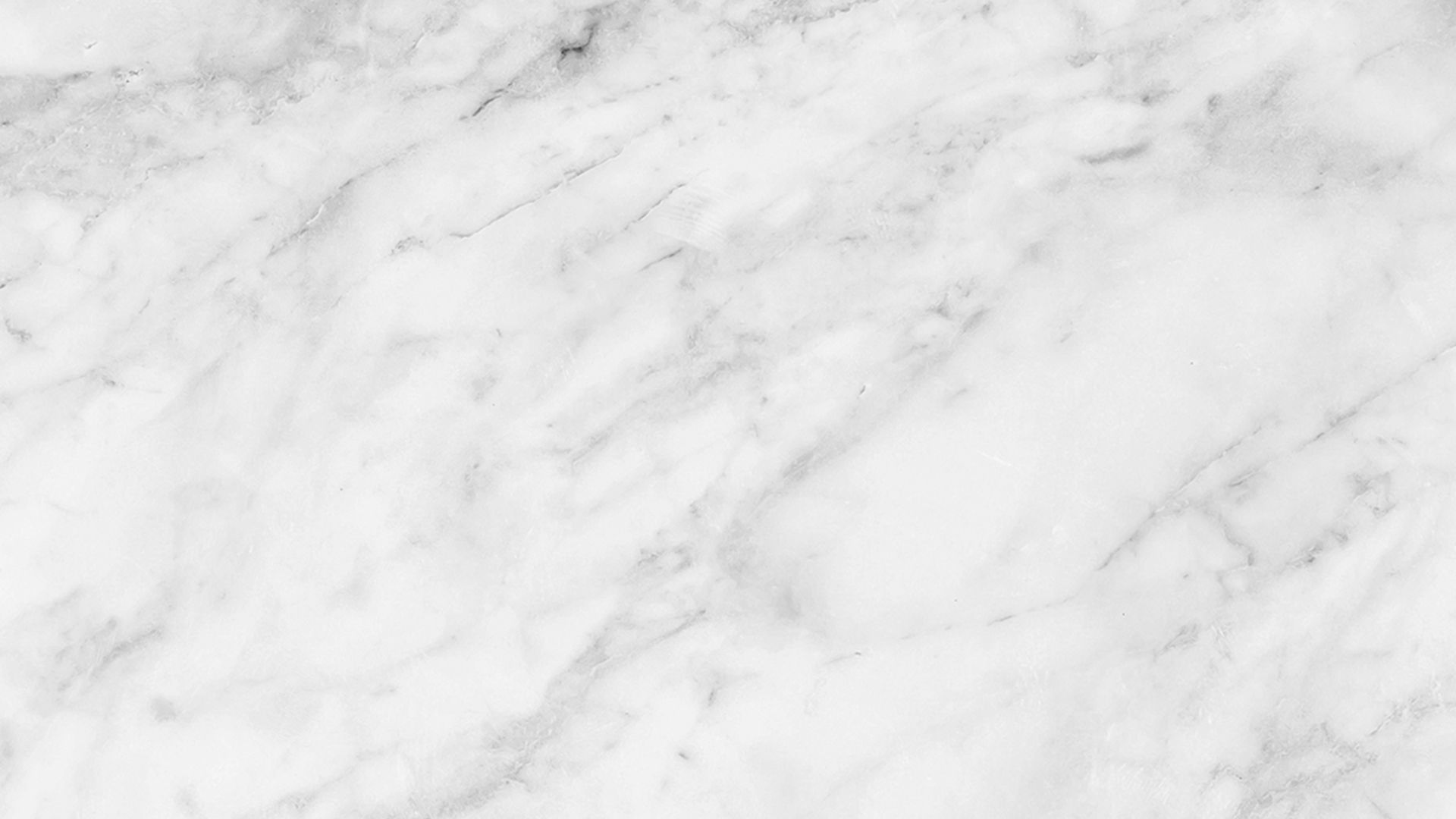
The Arundel at Arundel Preserve
Hanover, Maryland
Corey Mohar - Structural Option
Dr. Thomas Boothby

General Information
Owner:
Architect:
General Contractor:
Geotechnical Engineer:
Civil Engineer:
Structural Engineer:
MEP:
Accessibility Consultant:
Project Team
Project Name:
Occupancy Classification:
Size:
Number of Stories:
Height:
Project Delivery Method:
Cost:
Construction Duration:

The Arundel at Arundel Preserve
Residential
228,000 Square Feet
15
168 Feet
Design Bid Build
$43 Million
Feb. 2017 - Oct. 2018
Somerset Construction
Architects Collaborative, Inc.
The Whiting-Turner Contracting Co.
Geo-Technology Associates, Inc.
Morris & Richie Associates, Inc.
Kline Engineering & Consulting
Environetics
Steven Winter Associates
Architecture
The Arundels unique shape comes from the history of the lot. Originally, a bank was meant to be constructed on the site, and they had gotten so far as to start the building pad. However, soon after the project was abandoned. Instead, plans for a new residential structure were put in motion. As there was already a building pad layout, the architect decided to design using the shape of the already existing plan.
On the ground floor, residents and their guests are greeted by a large, open reception lobby, complete with a very unique lighting fixture consisting of frosted panels and LED lights. There is also a massive fish tank that runs along the corridor, inviting guests to observe with an interactive Ipad programmed to display information on the sea creatures inside. The tank is themed after the popular Disney movie, "Finding Nemo". Around the corridor guests can relax in the community lounge, which sports an enormous chandelier, and multiple television sets for residents to gather and socialize.
On the exterior, the Arundel utilizes a "tower feature" that separates the EIFs and the black brick on the side of the building pictured above. The glass starts at the first floor and continues straight up to the roof. The fifteenth floor opens out onto a rooftop terrace that has a few noteworthy features. Not only is there plenty of space to hang out and socialize the rooftop terrace has a specified area where residents can cook using the provided grill. There is also a gas fireplace that can be turned on for some of the more chilly evenings. Perhaps the most unique of the rooftop terrace's features is the life size chess board complete with massive chess pieces.
Codes
In the table to the left, all of the codes that were used in the design of The Arundel and its systems are listed. Additionally, ASCE 7-10 was referenced for the structural design of the building.
Based on the Anne Arundel County zoning map, the lot is mapped out as MXD-E. According to the county's zoning code, this is a Mixed Use area, however does not require any buildings be mixed use occupancies. Instead, it encourages owners to used mixed use by offering larger height and square footage allowances.

Building Enclosure
The Arundel has two primary facades; EIFS and brick and mortar. Each facade is framed using 4" metal studs, batt insulation and covered with 1/2" gypsum board on either side of the studs. The vapor barrier is a bituminous dampproofing material that is found behind all of the interior side drywall of the exterior walls. On approximately 80% of the building a 3 inch Exterior Insulation and Finish System (EIFS), with an elastomeric finish. The black brick is used mostly along the southern facade of the northern part of the building, as well as along the buildings parapet walls and first floor. The bricks are 4" and are non-structural.
The windows of the Arundel all use double pane 0.875" glass with a 0.625" air space between them to act as insulation. All of the window frames in the project are aluminum. The glazing is Molded Resilient Neoprene Gaskets, and uses EPDM as the spacers and setting blocks.
The storefront walls on the first wall are all anodized aluminum with reinforced mullions. Steel is used to help support the wall, rather than relying just on the primary structural floor framing to hang it. Curtain walls, located along the southern and western sides of the first floor, are glazed aluminum configurations that allow for thermal movement. Both systems are 1" thick double pane spandrel glass separated by 1/2" of air space.
For the roofing system, a typical Inverted Roof Membrane Assembly (IRMA) is used. The structural slab of the rooftop terrace is 12" thick and the edges leading up to parapet walls have a sloped concrete topping for drainage. Above the slab is 4" of rigid insulation, and a hot rubberized asphalt protective membrane acts as a waterproofing element. For a large portion of the terrace, 2" of gravel is the final layer. In high traffic, social, areas an exterior concrete tile is used.
Sustainability
For natural ventilation, all of the apartments have operable windows for residents to use on days where A/C is not necessary. In addition, the mechanical systems all have features to maximize efficiency such as temperature sensors to ensure that they cut off when the room reaches a desired temperature. They will resume only when necessary to maintain constant temperature. Much of the lobby uses LED lighting fixtures, which are of the highest life span, meaning less light bulbs and waste created from their use.
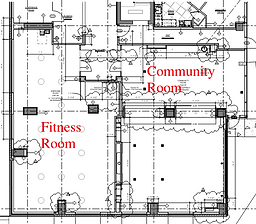



Primary Systems
Steel was set and materials hoisted to the upper extremities with the use of a crane at the beginning of the project. The two corner rooms on each floor of the north side of the building were intentionally left uncompleted in order to act as hoist units for materials. A lift system was incorporated to hoist materials up through these rooms as a more efficient means of transporting them to upper floors without having to block the elevators.
A Variable Refrigerant Flow (VRF) system is The Arundel’s source of air conditioning. The system is made up of 3 large rooftop air handling units as well as a single, smaller air handling unit in each residential room. Accompanying the rooftop units are 17 heat pumps.
The Arundel has three phase 120/277v power throughout the building. Each room has access to its own panel board to power each one separately. There are separate panels ever few floors to control the power to two or three floors at a time.
Lighting systems used range throughout the project building. A majority of the lighting fixtures in the back of house areas, such as the mechanical rooms, storage, maintenance and control rooms, are fluorescent. A few of the aesthetic lights in the lobby are incandescent with most of the lobby and corridor lights are LED.
A deep foundation system using 1/8” piles holds up a 4 foot thick transfer slab. The slab also rests on a grade beam that spans the perimeter of the building. For the other third of the building, a slab on grade is used, still on piles, and the columns are supported by 4 foot thick pile caps.
The gravity system is a post-tensioned two way slab system on isolated columns. #4 rebar @ 36” o.c. are used going east to west, while bundles, or bands, of post-tensioned cables run north to south, carrying significantly higher loads of tension across structural elements such as columns or shear walls.
For its lateral system, regular reinforced concrete load-bearing shear walls are used. Most of these make up the stairwells and elevator shafts, with one being a dividing wall between the units and first floor amenities.
Construction
Mechanical
Electrical/Lighting
Structural
Additional Systems
The thick concrete slabs that make up each floor provide a fire rating of at least 3 hours. The exterior walls all have a 2 ½ hour fire rating, with interior partitions being 1 hour rated. To minimize damage to the interior and to prevent any failure, sprinkler system is incorporated into the building. The bulk of the sprinkler heads are recessed into the ceiling, and set to deploy upon sensing smoke or extreme heat.
Fire Suppression